1. Projectile size
The larger the projectile, the greater the impact kinetic energy and the greater the cleaning intensity, but the coverage of the shot is reduced. Therefore, while ensuring the shot blasting strength, the smaller projectile should be selected as much as possible. In addition, the size of the shot peening is also limited by the shape of the part. When there is a groove on the part, the diameter of the shot should be less than half of the radius of the inner circle of the groove. The shot blasting size is often selected between 6 and 50 mesh.
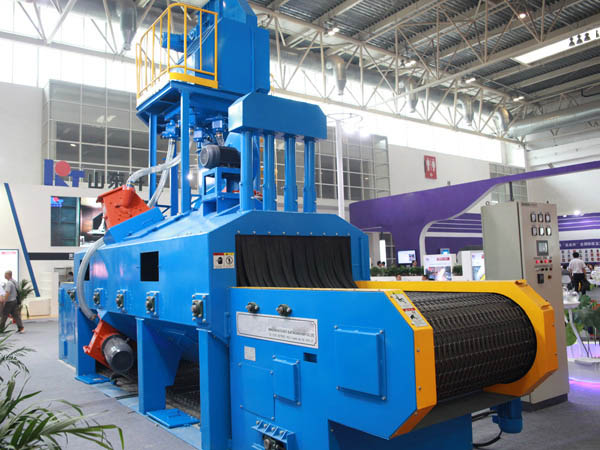
2. The hardness of the projectile
When the hardness of the projectile is higher than that of the part, the change of its hardness value does not affect the shot blasting strength.
When the specific hardness of the projectile is small, if shot blasting, the hardness value will decrease, and the shot blasting will also reduce the strength.
3. Shot blasting speed
When the shot blasting speed increases, the shot blasting intensity also increases, but when the speed is too high, the amount of shot damage increases.
4. Spray angle
When the shot blasting jet is perpendicular to the surface to be cleaned, the shot blasting intensity is high, so it should generally be kept in this state for shot blasting. If it is limited by the shape of the parts, when it is necessary to use a small angle of shot peening, the shot peening size and speed should be appropriately increased.
5 Fragmentation of the projectile
The kinetic energy of the projectile fragments is low, the more broken shot blasts, the lower the shot peening intensity, and the irregular broken shots will scratch the surface of the parts, so the broken shots should be removed frequently to ensure that the shot blasting integrity rate is greater than 85%. The shot blasting equipment is basically In the same way, only some auxiliary devices are needed to control the shot blasting process more strictly.
Post time: Aug-18-2023